LPC8 controller
Spark ignition engine management system, presently capable of fully sequential operation (injection and ignition) on engines with up to 8 cylinders. Based on the LPC4 but adds more I/O and features.
Developed in 2017, introduced in 2018.
A truly unique solution for its price class, developed with a philosophy of making it flexible in every part of the configuration while being intuitive to use, because it's up to the tuner to decide how they want to tune the engine.
Available for purchase from our web store
Specifications
Hardware specs
- Dual 32 bit microcontrollers
- External dimensions 115x106x46mm
- 8 dedicated injector outputs, 5A max current. Saturated (high-Z) injectors driven directly. Must use resistors for peak&hold (low-Z) injectors.
- 8 dedicated ignition outputs. Standard 5V logic level (50mA max) for smart coils or external ignition modules. Can be paired with ITM8 module for passive coils.
- 12 extra outputs suitable for PWM idle control, stepper idle control for 6 wire steppers, fuel pump relay control, tachometer output, boost control and more.
- Integrated bridge driver for electronic throttle control 15A peak current capacity.
- 2 dedicated engine speed inputs, support logic level and some VR sensors as standard. Modules available that install into the ECU to support weak signal VR sensors
- 5 extra inputs for cam timing sensors, road speed, turbocharger speed or frequency based MAF sensors. Can also be used as switch inputs
- 1 dedicated active low switch input
- Built in 4000mbar MAP sensor with 4mm push-lock bulkhead fitting. Suitable for up to 3 bar boost at sea level. MAP can also be taken from an unused analog input and external sensor, freeing the internal sensor for barometric correction.
- 3 dedicated 12 bit analog inputs for throttle position, engine coolant temperature and charge air temperature.
- 9 extra 12 bit analog inputs, selectable as lambda inputs, external MAP sensor, thermistors, pressure sensors, active low switches, multiplexed switches, calibration switch and more
- Built in lambda sensor interface with calibration resistor for Bosch LSU4.9 sensors with comprehensive sensor diagnostics and a dedicated lambda heater output. Can be calibrated to work with LSU4.2 or NGK sensors. External lambda controllers supported also.
- Dual knock sensors input with digital signal processing and time window rejection filtering. Keeps long term knock trims and adjusts timing on a per-cylinder basis.
- Powder coated extruded aluminium enclosure
- Conformal coated board for moisture/splash resistance, mounting in a dry location recommended nonetheless
- Molex mini-fit jr plastic crimp connectors
- CAN bus for interfacing with peripherals such as transmission control, dash displays, VGT actuators or sensor interfaces
- Native USB connection. No USB-232 converter or associated hassle.
- Data logging at over 50Hz standard via USB to computer running calibrator software
- 8GB Internal data logging memory standard with real time clock for time stamping of log files. Up to 500Hz data logging rate. Versatile logging conditions and burst logging.
- Operating internal temperature range -40°C to 100°C. Recommended that ambient temperature in mounting location does not exceed 60°C
- ECU temperature sensor integrated
- 2 years parts+labour warranty
Software feature highlights
- Advanced but ergonomic PC calibrator application.
- Fuelling and ignition maps with fully configurable dimensions up to 256 fields. (Can have for example 16 load breakpoints and 16 speed breakpoints, or 10 load breakpoints and 25 speed breakpoints). Do not settle for inferior controllers with fixed table dimensions.
- Fuel mass strategy with dual slope injector model for the ultimate control precision
- Electronic throttle control with friction control strategy for more precise operation at low throttle openings
- Cruise control (requires electronic throttle)
- NMEA input for GPS. Can use GPS ground speed for cruise control, traction control, transmission control, etc, with fall back to wheel speed possible when without GPS signal.
- Gear detection based on engine speed to wheel speed ratio
- Frequency based tachometer and speedometer output for instrument cluster (can calibrate speedometer in ECU)
- Idle speed control utilising dual control loop with ignition advance and idle valve working together
- Individual injector fuelling variation based on engine speed and load (up to 256 fields).
- Individual cylinder spark timing variation based on speed and load (up to 256 fields) if cam sync present, up to 8 cylinders
- Compatible with most crank/cam trigger arrangements found on engines today as well as tomorrow (fully user defined trigger patterns).
- Turbo boost control for any PWM operated pressure or vacuum solenoid, wide frequency range. Suitable for wastegated as well as VGT turbochargers.
- Unused extra outputs can be programmed as on-off based on all running parameters
- Firmware field upgradable over USB. No special hardware required. Firmware updates free of charge, new features still being developed.
- Long term fuel trims (automatic fine tuning of fuel map via lambda feedback)
- Long term knock trims (keeps track of under what conditions engine has been knocking and preemptively adjusts the ignition timing the next time those conditions are seen)
- Closed loop variable valve timing control of up to 4 camshafts
- Advanced nitrous oxide control strategy (2 stages, wet or dry, progressive PWM based on any parameter)
- Gear shift power reduction for clutched or clutchless upshifts
- Automatic transmission control for any sprag based automatic transmission (ie, not clutch to clutch), this includes most 4 speed and some 5 speed transmissions.
- Traction control that can use either GPS, undriven wheel speed or time after launch as slip reference.
- Industry leading CAN bus implementation. Lets the tuner configure CAN bus broadcast packet content to match almost any target device.
- Up to 8 different calibrations for most major functions selectable using one or up to four external switches (calibration pots)
- OBD2 over CAN bus for reading fault codes as well as sensor data. User defined OBD2 PIDs available for dash displays and such.
- Vast array of error detection functions and engine protection parameters. Fault codes kept in non-volatile memory and can be retrieved later either via Calibrator application or OBD2 interface.
- Vast array of user configurable functions (transfer functions, logic functions, latches, flip flops, counters, timers)
See user's manual
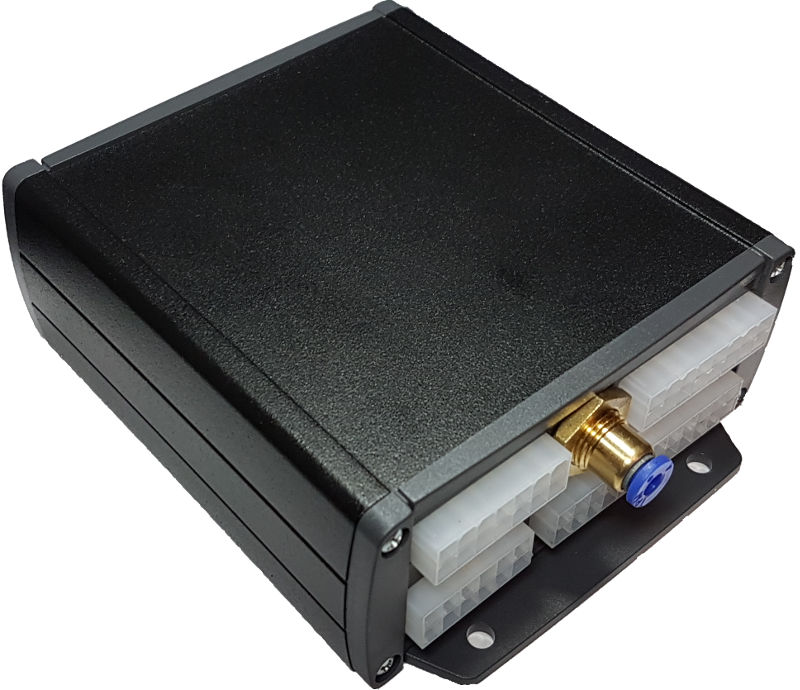
Back to main page